Ammonia-Free Process for Preparing Ammonium Metatungstate
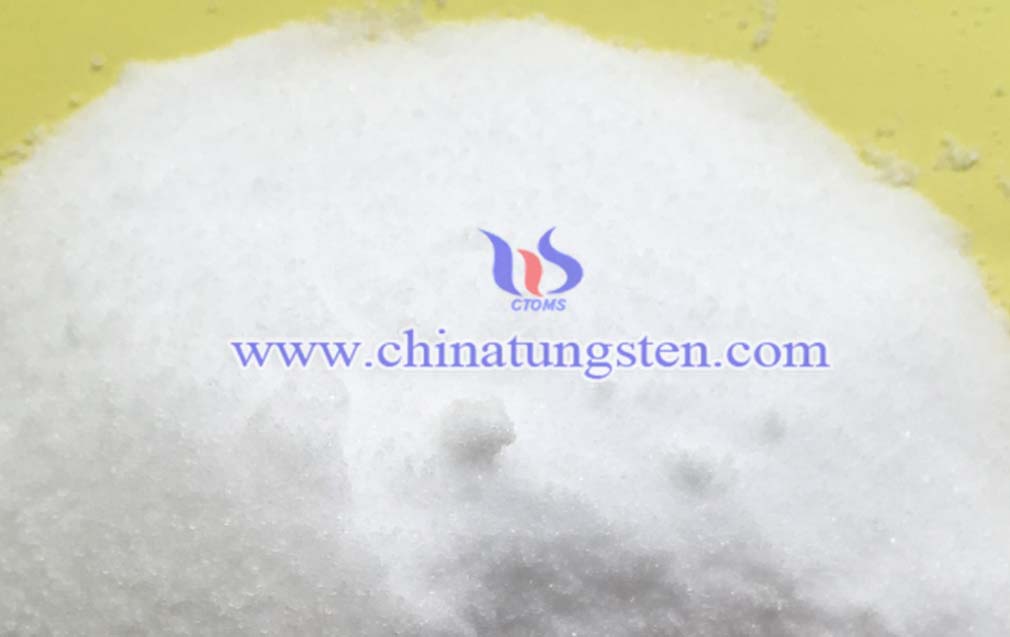
The ammonia-free process is an innovative green synthesis method aimed at directly preparing ammonium metatungstate (AMT) from sodium tungstate (Na₂WO₄), avoiding the use of ammonia water in traditional processes. This process employs physical or electrochemical methods to drive the polymerization of tungstate ions, significantly reducing ammonia emissions and the use of chemical reagents. Below is a detailed introduction to the two main technical approaches:
1. Electrochemical Method
The electrochemical method utilizes an electric field to drive tungstate ions (WO₄²⁻) to polymerize into AMT in an electrolytic cell, with the following characteristics:
• Working Principle: In the electrolytic cell, an electric field is applied to induce the polymerization of tungstate ions on specific electrode surfaces, forming AMT. The reaction produces minimal byproducts, primarily hydrogen (H₂) and oxygen (O₂), which can be easily collected and processed to achieve zero-pollution emissions.
• Advantages:
o Low Emissions: Eliminates the need for ammonia water, resulting in near-zero ammonia emissions.
o High Efficiency: Electric field regulation enhances reaction selectivity and yield, reducing side reactions.
o Controllability: By adjusting voltage and current density, the crystal structure and purity of AMT can be precisely controlled.
• Challenges: The choice of electrode materials and the design of the electrolytic cell significantly impact process efficiency and cost, requiring further optimization for large-scale production.
2. Ultrasonic Method
The ultrasonic method leverages the cavitation effect and mechanical vibrations of ultrasonic waves to promote the polymerization of tungstate ions, with the following characteristics:
• Working Principle: Ultrasonic waves generate localized high-temperature and high-pressure microbubbles (cavitation effect) in the solution, accelerating molecular collisions and polymerization of tungstate ions to form AMT.
• Advantages:
o Reduced Reaction Time: The physical effects of ultrasound can shorten the reaction time of traditional processes by 30%-50%.
o Reduced Reagent Use: Enhanced reaction efficiency significantly reduces the need for acidic reagents.
o Mild Conditions: The reaction typically occurs at lower temperatures and pressures, reducing energy consumption and equipment requirements.
• Challenges: The energy consumption and stability of ultrasonic equipment need further improvement to ensure long-term operational reliability.